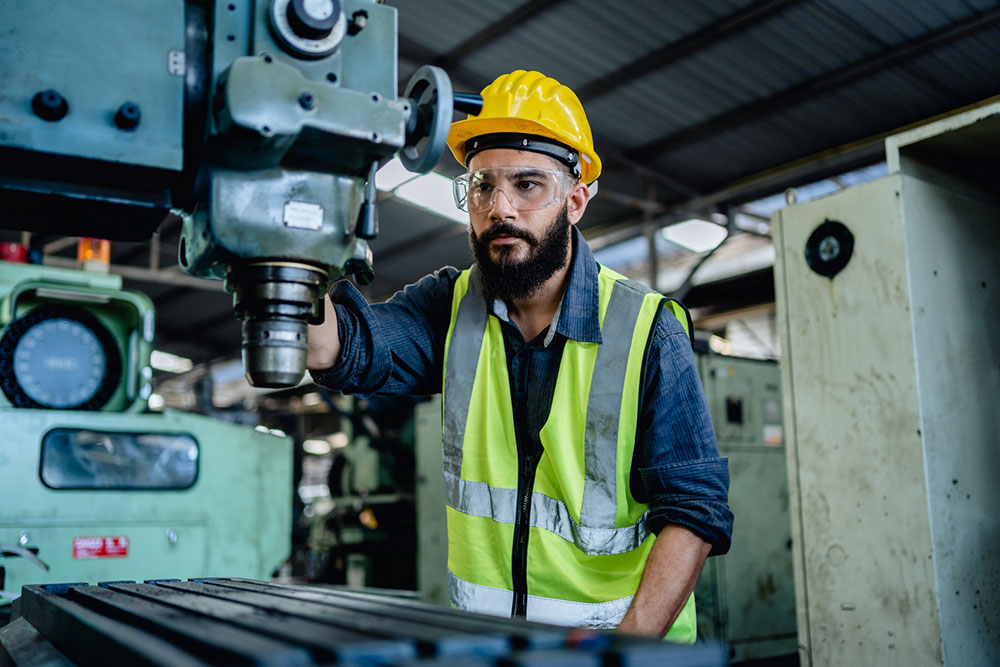
8 helpful tips for industrial machine maintenance
In the intricate tapestry of modern industries, machinery stands as an integral component across various sectors like mining, farming, and construction. Industrial machines form the backbone of production processes like manufacturing and processing. Therefore, it is important to maintain them in good condition to ensure they operate at their best capacity. Proper maintenance extends the lifespan of industrial machines and helps prevent costly breakdowns and downtime. Below are some tips to maintain their optimal performance.
Ensure proper lubrication
Friction in any machinery can lead to premature wear and tear, production delays, and loss of productivity. Lubrication is the process of applying a fluid or grease to reduce the friction between moving parts in a machinery. Lubrication also prevents corrosion and acts as a sealing and heat transfer agent. For smooth and optimal machine performance, it’s essential to adequately service and maintain the lubrication points. Check the high-speed spindles, motors, and oil levels. With lubrication, it’s also important to refer to the manufacturer’s guidelines and use the right kind of lubrication, like types of grease, solid oil, synthetic, chemical, or petroleum oil.
Check safety features
Regularly checking safety features such as emergency shutoff buttons, warning signs, and guard rails, down to tiny mechanical seals, is vital to prevent severe accidents in industrial settings. Neglecting their maintenance can jeopardize both personnel safety and equipment integrity.
Conduct regular inspections
Routine inspections are critical for identifying wear and tear, loose components, or any signs of malfunction. Inspect all machine parts, including belts, gears, bearings, and electrical components. Look for unusual sounds, vibrations, or leaks. Alternatively, one can also invest in sensors that track variables like temperature, vibration, and energy consumption.
Conduct calibration checks
Calibration involves adjusting and verifying the accuracy of measurement instruments in machinery. In industries requiring these types of machines, calibration checks are important. The frequency can vary based on the type of machine and usage, with some requiring more frequent assessments than others. When in doubt, one can hire a qualified technician to perform calibration tasks.
Note down usage and maintenance
One must maintain a comprehensive log of machine usage and maintenance activities. This detailed record helps monitor machine performance and identify areas requiring frequent service. The log can include information such as operational hours, the maintenance tasks performed, component replacements, and any issues encountered.
Develop a maintenance schedule
Creating a calendar that includes details like routine inspections, preventive measures, and other necessary repairs is one of the easiest ways to maintain industrial machinery. Consistency in scheduling allows one to identify potential issues on time before they escalate and cause unexpected breakdowns. A shared calendar also ensures that everyone is informed about the maintenance and employees do not start a machine just before it requires shutdown.
Understand the machine’s pressure points
Understanding the pressure points of the machine helps to anticipate certain machine issues. For instance, certain machine parts may endure more force or pressure during production and be more prone to cracking or warping. Knowing these pressure points and checking on them more often can reduce the likelihood of breakdowns.
Keep the space clean
Machines may get clogged or malfunction due to the accumulation of dust, debris, and other contaminants. It can affect their efficiency and even lead to breakdowns. So, clearing the workspace daily is important to avoid dirt build-up. It is especially advised for cooling systems or ventilators, which can overheat due to clogging and cause severe damage.